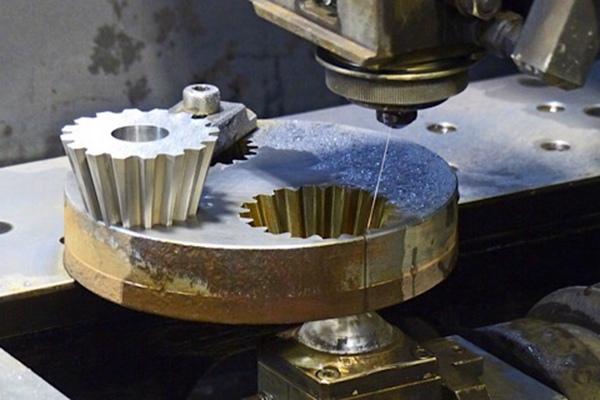
What is the Electrical Discharge Machining (EDM) Process
Electrical discharge machining (EDM) is a manufacturing process that uses electrical discharges (sparks) to remove material from a workpiece. EDM is used to create very precise shapes and holes in difficult-to-machine materials, making it a popular choice for machining delicate or intricate parts.
This process is often used to drill holes in hard or brittle materials. Drilling a hole with an EDM machine is a five-axis milling process that offers many advantages over traditional machining methods. With EDM hole drilling, there is no need for a pilot hole, and the versatile process can be used to machine a variety of materials, including aluminum, brass, and stainless steel. In addition, EDM hole drilling is relatively much faster than conventional drilling methods, making it a popular choice for manufacturing companies. And it produces very little heat, making it ideal for working with sensitive materials. Perhaps most importantly, EDM hole drilling produces very precise results, with tolerances of +/- 0.001″ or better. As a result, it is an increasingly popular choice for applications where precision is critical.
While EDM is typically used for industrial applications, it can also be used for hobbies and crafts. For example, EDM can be used to create custom holes in metal coins for jewelry making. To drill a hole with EDM, a small electrode is placed against the workpiece and a high-voltage current is passed between the electrode and the workpiece. The current causes the electrode to discharge sparks of electricity, which vaporize the metal and create a small hole. The size of the hole depends on the size of the electrode and the amount of time that the current is applied.EDM can be performed with a variety of different electrodes, including pointed, flat, and round electrodes. The type of electrode that is used will depend on the desired shape of the hole and the material that is being drilled. For example, pointed electrodes are often used to drill small holes in thin sheets of metal, while flat electrodes are better suited for drilling
Types of EDM
Die sinking EDM
What is die sinking electrical discharge machining? Die sinking electrical discharge machining is a process that uses an electrical current to remove material from a workpiece. The process works by passing an electric current through the workpiece, which ionizes the material and creates a plasma. This plasma then erodes the material away, leaving behind a cavity in the shape of the desired design.
The process is typically used to create intricate shapes or patterns that would be difficult to create using other methods. Die sinking EDM can be used on a variety of materials, including metals, plastics, and composites.
One advantage of die sinking EDM is that it can produce very precise results. The size and shape of the cavity created by the process can be controlled very precisely, making it possible to create complex shapes and patterns.
Additionally, die sinking EDM does not generate heat, so there is no risk of damaging the workpiece.Another advantage of die sinking EDM is that it can be used on a variety of different materials. This makes it a versatile tool that can be used for a wide range of applications. Die sinking EDM can be used to create medical implants, engine parts, and electronic components, among other things.
Wire EDM
Wire electrical discharge machining (WEDM) is a thermal machining process that uses a wire electrode to vaporize material from the workpiece. It is commonly used to cut hard or difficult-to-machine materials such as titanium, Inconel, and hastelloy. The WEDM process works by passing a thin wire electrode through the workpiece. As the wire passes through the workpiece, it emits sparks of electricity. These sparks vaporize small amounts of material from the workpiece, slowly cutting it into the desired shape.
WEDM is a very precise machining method and can produce parts with tight tolerances. It is also capable of machining very complex shapes that would be difficult or impossible to machine using other methods.
The main disadvantage of WEDM is that it is a slow machining process. It can take several hours to produce a single part, depending on its size and complexity. WEDM is also a relatively expensive machining method due to the cost of the wire electrode and the special equipment required. Despite these disadvantages, WEDM remains an important machining method for many industries where precision and complex shapes are required.
Hole drilling EDM
Hole drilling electrical discharge machining is a process that uses electrical discharges to remove material from a workpiece. This process is often used to drill holes in metals, but can also be used to machine other materials. Electrical discharge machining works by passing a high-voltage current through a workpiece. The current causes sparks to form between the electrode and the workpiece. These sparks erode the material, gradually removing it from the workpiece.Hole drilling EDM is typically used to drill small diameter holes in hard, brittle materials. This includes materials such as tungsten carbide, ceramic, and glass. Hole drilling EDM can also be used on softer metals, but it is not as effective as other methods such as drilling or milling.
The main advantage of hole drilling EDM is that it can produce very precise holes with smooth walls. This process is also relatively fast, making it ideal for high-volume production.Hole drilling EDM typically uses a cylindrical electrode to machine the workpiece. The electrode is mounted on a spindle and rotated at high speeds. As the electrode rotates, it emits electrical discharges that erode the material. The size of the hole that can be drilled using hole drilling EDM is limited by the size of the electrode. The depth of the hole is also limited by the power of the electrical discharge.
Hole drilling EDM is a versatile machining process that can be used to drill holes in a variety of materials. This process is particularly well suited for drilling small diameter holes in hard, brittle materials. Hole drilling EDM can also be used on softer metals, but is not as effective as other methods such as drilling or milling. The main advantage of hole drilling EDM is that it can produce very precise holes with smooth walls. This process is also relatively fast, making it ideal for high-volume production.
Conclusion
EDM is a unique machining process that has many benefits over traditional machining methods. It is more accurate, can produce complex shapes, and is very versatile. If you are looking for a precision machining method that can handle a wide variety of materials, EDM may be the perfect choice for you.
With a solid foundation in technology, backed by a BIT degree, Lucas Noah has carved a niche for himself in the world of content creation and digital storytelling. Currently lending his expertise to Creative Outrank LLC and Oceana Express LLC, Lucas has become a... Read more