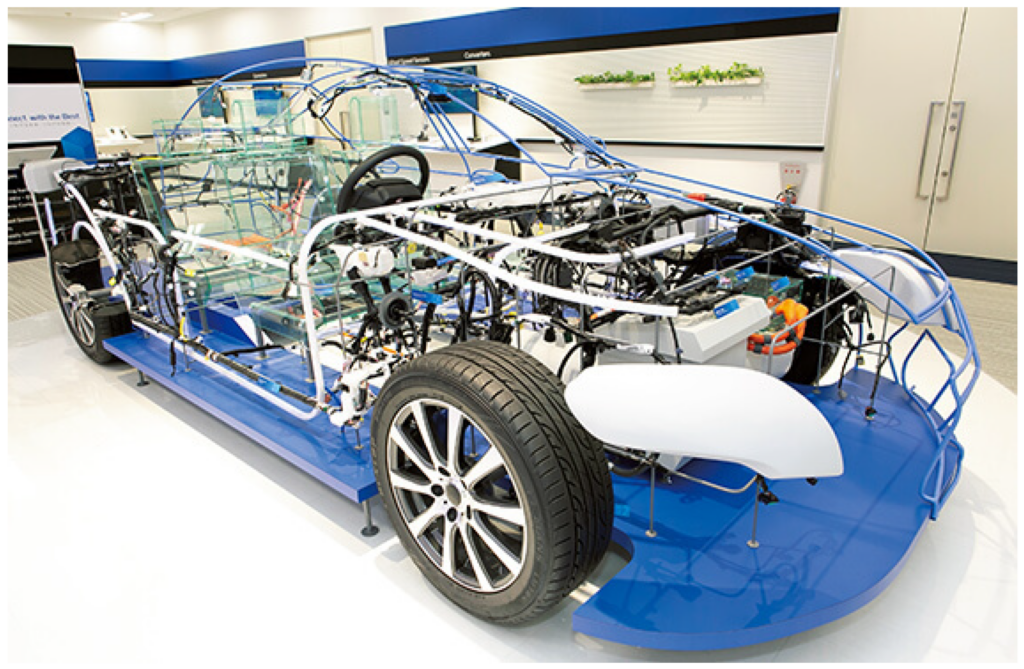
Using Precision to its Full Potential: Introduction to the Art of Wire Harness Assembly:
An essential step in the production of electrical and electronic goods is the assembly of the wire harness. It includes the careful incorporation of wires, connectors, terminals, and different parts to make a useful wiring framework. Because even a minor error can result in significant performance issues or safety risks, precision is essential during the assembly of wire harnesses. This article will discuss the importance of precision in wire harness assembly, the necessary tools and equipment, a step-by-step guide, common obstacles, efficient assembly tips, the advantages of mastering this art, and future trends in the field.
What exactly is Wire Harness Assembly?
Wire outfit get together is the most common way of sorting out and getting electrical wires and links into a sound framework. It involves arranging and connecting individual wires and cables to specific parts, as well as ensuring that the assembly is properly routed and protected. Automotive, aerospace, telecommunications, and consumer electronics are just a few of the industries where wire harnesses are utilized to provide electrical connectivity that is both dependable and effective.
Precision in Wire Harness Assembly Is Critical
For Several Reasons Precision is critical in wire harness assembly. First and foremost, the effective transmission of electrical signals is guaranteed by a properly assembled wire harness, lowering the possibility of signal loss or degradation. Second, precision assembly lowers the risk of wire damage or short circuits, which can cause electrical fires or malfunctions. Thirdly, precision is essential for complying with industry standards and regulations, ensuring product safety, and maintaining compliance. Lastly, the electrical system’s overall durability and longevity are enhanced by precise wire harness assembly.
Tools and Equipment for Wire Harness Assembly
Specific tools and equipment are required for wire harness assembly to be precise. These are some:
Wire strippers: used to remove insulation from the ends of wires so that they can be connected correctly.
Crimping devices: essential for securing the wire ends to terminals or connectors.
Cutter for wire: Used to slice wires to the ideal length exactly.
Copper solder: Required for connections made by soldering, which adds strength and dependability.
Heat-shrink tubing: used to shield wire connections from the elements and insulate them.
Link ties and clasps: Guarantee legitimate association and steering of wires inside the tackle.
Testing apparatus: incorporating continuity testers or multimeters to check the integrity of connections.
Wire Harness Assembly Step By Step Guide
Design and planning: Understanding the wire harness assembly’s requirements and specifications is the first step. Make a detailed schematic or diagram to use as a guide.
Choosing elements: Based on the application and the conditions of the environment, select the appropriate wires, connectors, terminals, and other components.
Prepare the wire: Using wire strippers, remove the insulation from the ends of the wires to ensure that the connections are the right length.
Pleating and binding: Using crimping tools or a soldering iron, adhere to industry standards for connecting the terminals or connectors to the wire ends.
Bundling and routing: Utilizing cable ties and clamps to secure the harness, arrange the wires and cables in accordance with the schematic.
Control of quality and testing: Use testing hardware to confirm the coherence and usefulness of the wire tackle gathering. In order to guarantee precision and accuracy, conduct thorough inspections.
Final setting up: Follow the instructions provided by the manufacturer as you insert the wire harness into the system or device that is being used.
Common Obstacles in the Assembly of Wire Harnesses:
Even though it’s important, putting together a wire harness can be hard. Common problems include:
Erroneous wire directing or associations, prompting ill-advised usefulness.
wire fatigue or damage as a result of inadequate strain relief or protection
inadequate insulation, which can cause electrical hazards or short circuits.
inconsistent crimping or soldering, resulting in connections that are unreliable or weak.
difficulties in identifying and fixing malfunctioning wire harnesses.
Effective Wire Harness Assembly Hints:
Consider the following recommendations to ensure efficiency and streamline the assembly of wire harnesses:
To make maintenance and assembly simpler, use connectors and components that are standard.
Improve precision and dependability by spending money on high-quality tools and equipment.
Educate assembly staff on industry standards and best practices.
Implement strict measures for quality control, such as regular testing and inspections.
Utilize feedback and analysis to continuously enhance assembly procedures.
The Advantages Of Mastering Harness Assembly:
There are numerous advantages to mastering wire harness assembly provided by pcb assembly manufacturer for both manufacturers and end users. These are some:
improved product performance and dependability as a result of precise electrical connections.
Further developed assembling proficiency through smoothed out gathering processes.
Cost savings by lowering the number of rework jobs, warranty claims, and potential recalls.
Product safety is ensured by compliance with industry regulations and standards.
Upper hand through the conveyance of excellent and solid items.
Trends in Wire Harness Assembly for the Future:
The demands of the market and advancements in technology are driving the ever-evolving field of wire harness assembly. The following are some new trends:
Robots and automation: increasing the integration of automated systems for assembly that is both faster and more precise.
Miniaturization: reducing the size of wire harnesses to accommodate electronic devices that are smaller and more intricate.
Connectivity via wireless: utilizing wireless technologies to reduce the use of conventional wired harnesses.
Savvy saddles: Wire harnesses that incorporate sensors and data communication capabilities for improved monitoring and diagnostics
Conclusion:
If you want to make electrical products that are both dependable and efficient, you need to know how to put wire harnesses together well. In order to achieve optimal functionality, safety, and compliance with industry standards, precision is essential. Manufacturers can benefit from precise wire harness assembly if they adhere to the step-by-step guide, address common issues, and employ effective assembly techniques. To remain competitive and meet the needs of electrical systems of the future, it will be essential to embrace emerging trends as the industry continues to change.