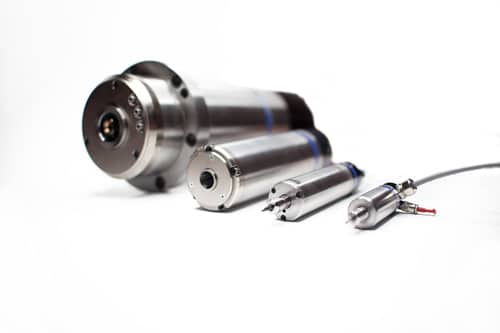
High Speed Precision Spindles: Features and Maintenance Tips
High-speed spindles are a critical component in CNC machines and the backbone of high-speed machining (HSM) operations. If your spindles aren’t well maintained, they’ll wear and fail faster than they should, putting your operations at risk and leading to higher costs and unnecessary downtime.
A robust and active maintenance program ensures your spindles provide the precision products your customers expect. Such a program also means having a complete understanding of all the features and components that are associated with spindles for a CNC machine. With this understanding, you’ll also be able to apply our maintenance tips and keep your spindles operating at high speeds and delivering precision products the way they’re designed to.
Spindle Unit
The spindle unit within a CNC machine acts as the workhorse for any HSM operation. Like any machine that operates at high speeds, several features and components directly support the rotational element to ensure it functions efficiently, precisely, and reliably. In the case of CNC machine spindles, those features include:
- Spindle Shaft. When discussing a spindle unit, you should first consider the high-speed shaft. This part of the unit must be properly balanced, aligned, and maintained to avoid delivering flawed products, leading to downtime and rework.
- Motor and Transmission. The choice of spindles usually comes down to two types: belt-driven and motorized. Both rely on motors to provide the rotational energy of the spindle shaft. However, as you can imagine, the belt-driven type is driven by a belt acting as the transmission between the motor and the shaft. On the other hand, motorized spindles have their motors coupled directly to the shaft, reducing the space needed for the unit and increasing power transmission efficiency within the CNC machine.
- Bearings. Spindle units also rely on precision bearings to support the rotation and weight of the high-speed shaft. These bearings ensure proper operation while helping maintain balance and alignment. Lastly, they absorb radial, axial, and thrust loads to help prolong the life of the spindle unit.
- Cooling and Lubrication Systems. Cooling and lubrication support with spindle-bearing grease are required to prevent overheating, parts seizing, component failures, and equipment damage.
- Toolholders and Drawbars. There wouldn’t be much use for spindles if there weren’t a tool holder that held the tool doing the material removal. In the case of spindles, those include cutting, grinding, drilling, and milling tools, to name a few. The drawbar acts as the clamping mechanism for the tool holder.
- Automatic Tool Changer (ATC). Not every CNC machine has a spindle with an automatic tool changer. However, ATCs are common for high-production operations and increase production efficiency by eliminating the need for an operator to continuously change tools.
Maintenance Tips for Spindles for a CNC Machine
Now that we have discussed the common features of spindles, let’s dive into the maintenance tips that can help keep your spindle and its components operating efficiently and reliably. Some of these will seem obvious. However, the obvious ones are sometimes the most overlooked or ignored if laziness or lack of attention to detail takes hold.
Administer a Routine Maintenance Program
A routine maintenance program will incorporate many of the tips we’ll mention here, along with periodic maintenance that should be incorporated based on run hours, type of work, and operational conditions. Routine maintenance that operates as both preventive and predictive maintenance (using tools like vibration analysis) will be the biggest step you can take in ensuring your equipment runs faster, longer, and more efficiently for years to come.
Train Your People
It’s one thing to have an effective maintenance program in place. It’s another to have a training program that ensures your operators and technicians know how to maintain your equipment and peak operating capability. You can’t have reliable machines and poorly trained people. The two simply don’t go together.
Conduct Regular Inspections
Yes, you should always inspect the condition of your spindle assemblies. Yet you should also inspect the performance of your operators and technicians. Make sure they operate and repair your spindles how they’re designed. Don’t tolerate pushing equipment to failure when simple repairs can be made, even if it means some downtime. And don’t avoid making repairs out of fear of lost time and increased costs. Doing so will actually hurt your profits in the long run.
Maintain Your Spindle’s Balance and Alignment
Again, don’t push your machines to the point of failure. In addition, don’t overload them or sacrifice quality for speed and numbers. Keeping your equipment balanced and aligned will ensure your products have the expected final quality and meet all precision requirements.
Keep Your Equipment and Workspaces Clean
A lot of damage and repairs can be avoided simply by keeping a safe and clean work environment. Don’t allow debris, dirt, and corrosion to build up to the point that it negatively affects your machines’ performance and material condition.
Monitor your Lubrication and Cooling Systems
Keeping both systems squared away will minimize damage from wear, friction, and overheating to your spindles. They’ll also maintain system performance and precision while increasing its potential lifespan.
Sharpen Your Tools and Replace Them as Necessary
Your spindles can’t be reliable workhorses without sharp and well-maintained tools. Wear and tear of tools is unavoidable. Keep them sharp for as long as possible, but don’t hesitate to replace them when needed.
Maintain a Stable Supply of Repair Parts
One of the most effective ways to keep your operations running smoothly is to keep an adequate stock of repair parts and components. It’s easier to reduce downtime and rework if repairs are necessary if you already have the new parts handy.
In Conclusion
Spindles come with several critical features that make high-speed machining precise, efficient, and reliable. Proper maintenance, quality training, attention to detail, and timely repairs and replacements are all essential to keeping your HSM operations flowing. In the end, though, downtime and unexpected costs may be unavoidable to ensure the precision of your products remains constant. However, following our tips above will make such instances few and far between.
With a solid foundation in technology, backed by a BIT degree, Lucas Noah has carved a niche for himself in the world of content creation and digital storytelling. Currently lending his expertise to Creative Outrank LLC and Oceana Express LLC, Lucas has become a... Read more