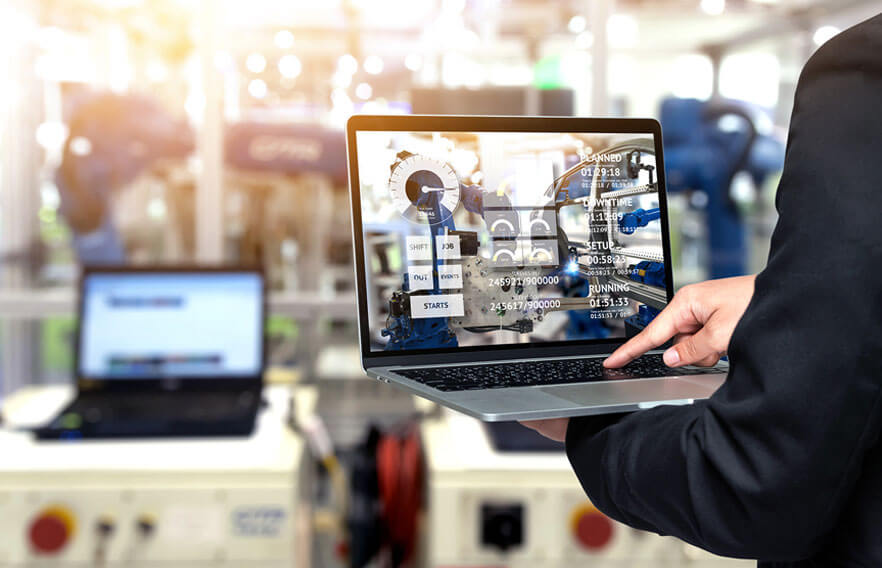
Data Analytics in Manufacturing
When manufacturers want to improve productivity and achieve the strategic goals, they often start with advanced analytics tools. These technologies can help with the most valuable working processes and decision making for the companies process change.
Data analytics experts will help manufacturing companies uncover and understand the nuances of their specific business and process areas https://cobit-solutions.com/en/5-main-power-bi-reports-in-manufacturing-company/. Moreover data analytics in manufacturing will present findings in ways that will be meaningful to the users businesses are trying to reach.
Predictive Maintenance
Predictive maintenance is a proactive approach to equipment management that uses data analytics to help companies detect issues before they turn into serious problems. This helps keep equipment working properly, increasing productivity and minimizing costs.
Many manufacturers and fleets use predictive maintenance technology to help reduce downtime, fuel consumption and service costs. This is especially true for heavy machinery, which often can be located far away from maintenance teams and engineers.
Condition-monitoring devices, vibration analysis, thermal imaging, sonic acoustical analysis, and oil analysis are all technologies that may be used for predictive maintenance. IoT translates information from these sensors into digital signals that can be analyzed to predict when an asset needs maintenance.
Using predictive maintenance is a smart decision for manufacturers and fleets with expensive equipment. It allows them to make sure they are implementing the best maintenance practices and using only the most effective parts. This can save money on spare parts and supplies, as well as avoiding unexpected breakdowns and repairs that aren’t needed.
Maintenance Scheduling
In manufacturing, efficiency is one of the core values, and unscheduled downtime can severely impact production. Luckily, with data analytics in place, manufacturers have real-time insights to improve their processes and make smart adjustments in their operations.
To start, it’s important to create a scheduling master document that lists all of the critical variables your maintenance team needs to consider. It should include information like your facility’s schedule board, the availability of technicians and their skills set, your prioritization table and any other relevant data.
Once you have this info in place, you can begin scheduling work orders with confidence. Ideally, your maintenance team will complete these tasks at the scheduled date and time, but that’s not always possible.
When work orders are pushed back, the SMCP can help your maintenance team prioritize which ones to tackle first. However, SMCP is only one metric you should use to determine which overdue tasks should be tackled first. It’s still necessary to consider all the other variables we covered earlier.
Quality Control
Quality control is a vital part of manufacturing, and data analytics helps ensure that products are up to par with standards. This means that you can prevent failures before they happen, reducing costs and avoiding field complaints.
As the Fourth Industrial Revolution continues to make its way into manufacturing, the ability to collect and analyze data in real time has become essential. This allows manufacturers to create end-to-end connected value chains that are more sustainable, agile and efficient, and to drive a better customer experience (Belhadi et al., 2019).
Data analytics in manufacturing can also help to streamline warehouse operations and product fulfillment. For example, data gleaned from demand forecasting can be used to identify which manual processes are more likely to cause mistakes in order fulfillment. This can be used to proactively automate processes and optimize staffing needs during busy periods. It can also be used to uncover consistent patterns in errors that need to be addressed.
Operational Efficiency
Operational efficiency is a vital business strategy that can help businesses achieve higher income levels while cutting down on operating costs. This metric is often used to measure the overall profitability of a company by comparing the net income generated with the expenses incurred.
If you’re a manufacturer, you’ve likely been using a variety of tools to improve operational efficiency. These include deploying more automation, improving workflows, and updating processes.
These improvements can lead to a number of benefits, including increased productivity, streamlined operations, improved quality, and reduced cost. Moreover, they can also increase employee satisfaction and customer loyalty.
The key to optimizing production throughput is capturing, cleansing and analyzing machine data from all sources. This data can then be used to predict and address problems that create bottlenecks in production. It may also be used to identify and eliminate unplanned production outages that can take a manufacturing line offline for days or longer.
With a solid foundation in technology, backed by a BIT degree, Lucas Noah has carved a niche for himself in the world of content creation and digital storytelling. Currently lending his expertise to Creative Outrank LLC and Oceana Express LLC, Lucas has become a... Read more